A pelletáló gép egy biomassza pellet tüzelőanyag és pellet adagolás sűrítésére szolgáló eszköz, amelynek fő alkotóeleme és egyben sérülékeny része a nyomógörgő. Nagy munkaterhelése és zord munkakörülményei miatt, még kiváló minőség esetén is elkerülhetetlen a kopás. A gyártási folyamat során a nyomógörgők fogyasztása magas, ezért a nyomógörgők anyaga és gyártási folyamata különösen fontos.
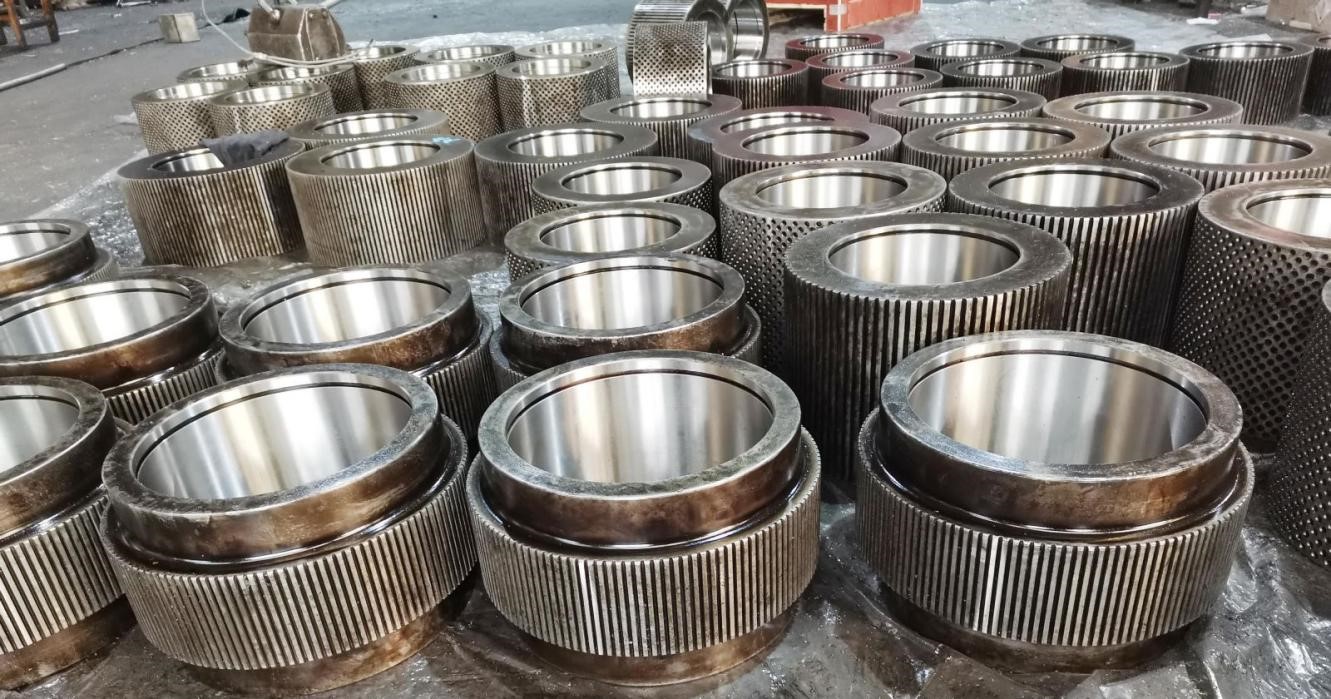
A részecskegép nyomógörgőjének meghibásodási elemzése
A nyomóhenger gyártási folyamata a következőket foglalja magában: vágás, kovácsolás, normalizálás (lágyítás), durva megmunkálás, edzés és temperálás, félprecíziós megmunkálás, felületedzés és precíziós megmunkálás. Egy profi csapat kísérleti kutatást végzett a biomassza pellet tüzelőanyagok gyártási és feldolgozási kopásáról, elméleti alapot teremtve a hengeranyagok és hőkezelési folyamatok racionális kiválasztásához. A kutatás következtetései és ajánlásai a következők:
A granulátor nyomógörgőjének felületén horpadások és karcolások jelennek meg. A nyomógörgőn lévő kemény szennyeződések, például homok és vasreszelék kopása miatt ez a rendellenes kopásnak minősül. Az átlagos felületi kopás körülbelül 3 mm, és a kopás mindkét oldalon eltérő. Az adagoló oldalon erős kopás tapasztalható, 4,2 mm-es kopással. Ez főként annak köszönhető, hogy az adagolás után a homogenizátornak nem volt ideje egyenletesen eloszlatni az anyagot, és belépett az extrudálási folyamatba.
A mikroszkopikus kopásvizsgálat azt mutatja, hogy a nyomógörgő felületén az alapanyagok által okozott axiális kopás miatt a nyomógörgő felületi anyagának hiánya a meghibásodás fő oka. A kopás fő formái az adhéziós kopás és az abrazív kopás, amelyek morfológiája olyan, mint a kemény gödrök, ekegerincek, ekehornyok stb., ami azt jelzi, hogy a nyersanyagokban található szilikátok, homokszemcsék, vasreszelék stb. komoly kopást okoznak a nyomógörgő felületén. A vízgőz és más tényezők hatása miatt iszapszerű mintázatok jelennek meg a nyomógörgő felületén, ami feszültségkorróziós repedéseket eredményez a nyomógörgő felületén.
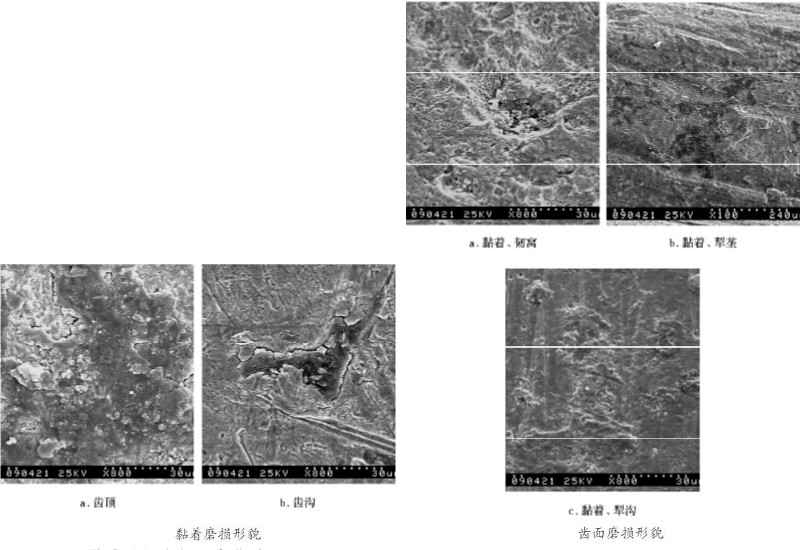
A nyersanyagok zúzása előtt ajánlott szennyeződés-eltávolítási folyamatot végezni a nyersanyagokban kevert homokszemcsék, vasreszelék és egyéb szennyeződések eltávolítására, hogy megakadályozzuk a nyomógörgők rendellenes kopását. A kaparó alakját vagy beépítési helyzetét úgy kell megváltoztatni, hogy az anyag egyenletesen oszoljon el a nyomókamrában, megakadályozva a nyomógörgőre ható egyenetlen erőhatást és a nyomógörgő felületének kopását. Mivel a nyomógörgő főként a felületi kopás miatt meghibásodik, a nagy felületi keménység, kopásállóság és korrózióállóság javítása érdekében kopásálló anyagokat és megfelelő hőkezelési eljárásokat kell választani.
A nyomógörgők anyag- és folyamatkezelése
A nyomóhenger anyagösszetétele és gyártási folyamata előfeltétele a kopásállóság meghatározásának. A leggyakrabban használt hengeranyagok közé tartozik a C50, 20CrMnTi és GCr15. A gyártási folyamat CNC szerszámgépeket használ, és a henger felülete az igényeknek megfelelően testreszabható egyenes fogakkal, ferde fogakkal, fúrási típusokkal stb. A henger deformációjának csökkentése érdekében karbonizációs edzést vagy nagyfrekvenciás edzéses hőkezelést alkalmaznak. A hőkezelés után precíziós megmunkálást végeznek a belső és külső körök koncentrikusságának biztosítása érdekében, ami meghosszabbíthatja a henger élettartamát.
A hőkezelés fontossága a nyomóhengereknél
A nyomóhenger teljesítményének meg kell felelnie a nagy szilárdság, a nagy keménység (kopásállóság) és a nagy szívósság, valamint a jó megmunkálhatóság (beleértve a jó polírozást) és a korrózióállóság követelményeinek. A nyomóhengerek hőkezelése fontos folyamat, amelynek célja az anyagokban rejlő lehetőségek kiaknázása és teljesítményük javítása. Közvetlen hatással van a gyártási pontosságra, a szilárdságra, az élettartamra és a gyártási költségekre.
Ugyanazon anyag esetében a túlhevítésen átesett anyagok sokkal nagyobb szilárdsággal, keménységgel és tartóssággal rendelkeznek a túlhevítésen át nem esett anyagokhoz képest. Ha nem edzik, a nyomógörgő élettartama sokkal rövidebb lesz.
Ha különbséget szeretnénk tenni a hőkezelt és a nem hőkezelt, de precíziós megmunkáláson átesett alkatrészek között, lehetetlen pusztán a keménység és a hőkezeléses oxidációs szín alapján megkülönböztetni őket. Ha nem szeretnénk vágni és vizsgálni, megpróbálhatjuk megkülönböztetni őket kopogáshanggal. Az öntvények és a megeresztett munkadarabok metallográfiai szerkezete és belső súrlódása eltérő, és finom kopogtatással megkülönböztethető.
A hőkezelés keménységét számos tényező határozza meg, beleértve az anyagminőséget, a méretet, a munkadarab súlyát, alakját és szerkezetét, valamint a későbbi feldolgozási módszereket. Például, ha rugós huzalt használnak nagy alkatrészek gyártásához, a munkadarab tényleges vastagsága miatt a kézikönyv szerint a hőkezelési keménység elérheti az 58-60 HRC-t, amit a tényleges munkadarabokkal kombinálva nem lehet elérni. Ezenkívül az ésszerűtlen keménységi mutatók, például a túlzottan magas keménység, a munkadarab szívósságának csökkenéséhez vezethetnek, és repedéseket okozhatnak használat közben.
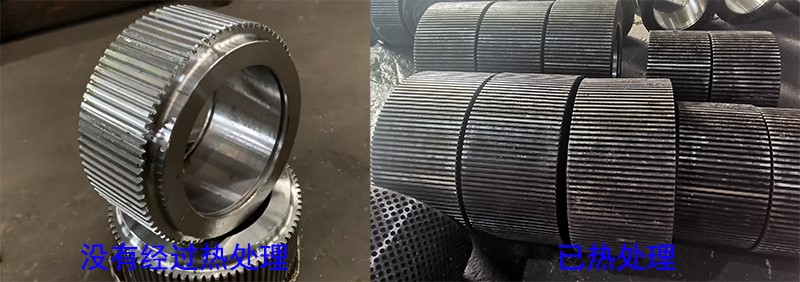
A hőkezelésnek nemcsak a minősített keménységi értéket kell biztosítania, hanem a folyamatválasztásra és a folyamatszabályozásra is figyelmet kell fordítania. A túlmelegített edzés és megeresztés elérheti a kívánt keménységet; hasonlóképpen, a hevítés alatti edzés során a megeresztési hőmérséklet beállításával is elérhető a kívánt keménységi tartomány.
A Baoke nyomóhenger kiváló minőségű C50 acélból készül, ami biztosítja a részecskegép nyomóhengerének keménységét és kopásállóságát a forrástól kezdve. A kiváló magas hőmérsékletű edzéses hőkezelési technológiával kombinálva jelentősen meghosszabbítja élettartamát.
Közzététel ideje: 2024. június 17.